Hand Tapping on a Drill Press
Tapping by hand on a drill press is usually accomplished by drilling
the part with a tap drill, then placing a 60-degree straight shank center,
or spring center (Figure 1), in the drill chuck. |

Figure 1 Spring center
|
The tap, in a tap wrench, is placed in the hole to be tapped and
aligned by placing the center in the center hole of the tap or the tap
wrench. By applying pressure to the center while turning the tap, the
internal thread is cut square to the workpiece (Figure 2).
Figure 2 Hand tapping
on a drill press
|
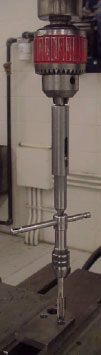 |
Machine Tapping on a Radial Drill Press
Tapping on a radial drill press is accomplished by either placing the tap in
the tap driver (Figure 3) or in a drill chuck (Figure 4). A relatively
slow speed is used to tap, and when the tap is through far enough, the
spindle clutch is reversed and the tap is backed out. As the tap is being
backed out, maintain a light upward pressure to keep the tap from
destroying the first two or three threads. |
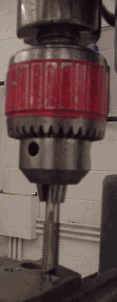
Figure 4 Machine tapping with
a drill chuck
|
 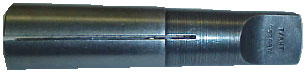
Figure 3 Tap driver
|
Cutting Speeds for Machine Tapping
There are many variables that must be considered when machine tapping.
Selecting cutting speeds for tapping is not done as easily as it is in
other machining operations. The best and most efficient cutting speeds for
tapping are selected by keeping in mind these factors:
- Material to be tapped
- Length of the hole
- Length of the chamfer at the top of the hole
and the length of the chamfer on the tap
- Pitch of the thread
- Percentage of full thread to be cut
- Cutting fluid to be used
- Sensitivity and rigidity of the machine
For example, cutting speeds must be lowered as the depth of the hole is
increased because of chip evacuation problems, and because of the
intermittent flow of cutting fluids. Taps with large starting chamfers can
be run at faster cutting speeds; however, taps with shorter chamfers can be
run faster in deeper holes. Bottoming taps must be run slower than plug
taps or taper taps. A slower speed is used on taps that cut a greater
percentage of threads. Coarse thread taps must be run slower than taps
with a fine pitch. The machinist must exercise judgment when deciding the
cutting speed limits as compared to his or her ability to control the
machine in order to prevent tap breakage. A table of recommended cutting
speeds for tapping is given below; however, the machinist must make
adjustments according to the factors that were just discussed.
Table 5 Cutting Speeds for Machine Tapping
Material
|
Cutting Speed, fpm |
Material
|
Cutting Speed, fpm |
Low Carbon Steels
Up to .25% C
Medium Carbon Steels
.30 to .60% C
Annealed
Heat Treated
(220 to 280 Bhn)
Tool Steels, High Carbon
and High-Speed Steel
Stainless Steels
Gray Cast-Iron
Malleable Iron
Ferritic
Pearlitic
Zinc Die Castings |
40 to 80
30 to 60
20 to 50
20 to 40
5 to 35
40 to 100
80 to 120
40 to 80
60 to 150
|
Aluminum
Brass
Manganese Bronze
Phosphor Bronze
Naval Brass
Monel Metal
Tobin Bronze
Plastics
Thermoplastics
Thermosetting
Hard Rubber
Bakelite |
50 to 200
50 to 200
30 to 60
30 to 60
80 to 100
20 to 40
80 to 100
50 to 100
50 to 100
50 to 100
50 to 100 |
Tapping Attachments
When tapping is done on a drill press, there must be some
way to back the tap out of the hole. Most radial drills are equipped
with a reversing spindle. Upright and sensitive drill presses are not
usually equipped with spindle reversing capabilities, thus a special attachment for
this operation is required.
An automatic reversing tapping attachment (Figure 6) has a tapered
sleeve that is inserted into the spindle of the drill press. When tapping
a hole using a tapping attachment, the tap is lowered into the hole and
fed to the proper depth manually.
|
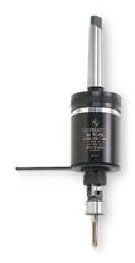
Figure 6 Tapping attachment
|
When the drill press spindle is raised, gears within the tapping
attachment are engaged, causing the tapping head to reverse, quickly
backing the tap out of the hole. The tapping attachment can also be
equipped with adjustable friction drives that stop the rotation of the tap
whenever the tapping torque exceeds a pre-set torque limit, thus keeping
the tap from breaking.
|