Cutting Fluid Types and Uses
|
Cutting fluids are very important in machining processes. They are used to
reduce the effects of friction. They are also used to carry away heat in
machining operations. Excessive heat can damage the microstructure of metals.
Proper use of coolants can make higher metal removal rates possible. Coolants can
also help improve part quality and dimensional accuracy.
The student will be able to:
- Explain the importance of cutting fluids in machining.
- Explain the common types of coolants available.
- Select the proper coolant for various machining operations.
There is a wide variety of cutting fluids available today. Many new coolants
have been developed to meet the needs of new materials, new cutting tools, and
new coatings on cutting tools. The goal of machining operations must be to
improve productivity and reduce costs. This is accomplished by machining at the
highest practical speed while maintaining practical tool life, reducing scrap,
and producing parts with the desired surface quality. Proper selection and use
of cutting fluids can help achieve all of these goals.
In machining almost all of the energy expended in cutting is transformed into
heat. The deformation of the metal to create chips and the friction of the chip
sliding across the cutting tool produce heat. The primary function of cutting
fluids is to cool the tool, work piece, and chip, reduce friction at the sliding
contacts, and prevent or reduce the welding or adhesion on the contact
edges that causes a built-up edge on the cutting tool or insert. Cutting fluids
also help prevent rust and corrosion and flush chips away.
Most shops try to reduce the number of different types of fluids that they
keep in stock. They try to stock fluids that have long-life, do not need to be
changed constantly, don’t smoke in use, and don’t cause skin irritation. One
large consideration is disposal. It is very costly to
dispose of cutting fluids.
Cutting Fluid Purposes
 |
Cooling
Machining operations create heat. This heat must be removed from the process.
The chip helps carry away heat from the tool and work piece. Coolant takes heat
from the chips tool, and work piece. To be effective the fluid must be able to
transfer heat very rapidly. The fluid absorbs the heat and carries it away.
Lubrication
In a typical machining operation, two-thirds of the heat is created by the
resistance of the work piece atoms to being sheared. The friction of the chip
sliding over the cutting tool face creates the other one-third of the heat.
Cutting fluid with good lubrication qualities can reduce the friction of the
chip sliding over the tool face. The lubrication actually changes the shear
angle, which reduces the shear path and produces a thinner chip. Good
lubrication also reduces internal friction and heat through less molecular
disturbance.
Benefits - Effective use of coolants
Improve Part Quality |
The use of cutting fluids reduces friction and heat. The removal of the
heat prevents the work piece from expanding during the machining
operation, which would cause size variation as well as damage to the
material’s microstructure. |
Reduce tooling costs |
Proper use of cutting fluids increases tool life, which reduces the
tooling costs. Increased tool life also reduces tool changes and downtime
which decreases labor costs. |
Increase Cutting Speeds and Feeds |
Cutting tools reduce friction and heating a machining operation. This
allows high speeds and feeds to be used to achieve optimal cutting
conditions. |
Improved Surface Finishes |
Effective use of cutting fluids helps remove the chips. This prevents
the chip from being caught between the tool and work piece where it causes
scratches and a poor surface finish |
Reduces Bacterial Growth |
Bacteria can drastically affect cutting oils. Bacteria growth can turn a
cutting fluid rancid. Additives in coolants help reduce the effects of
bacteria, but it is important that pure water is used for coolant mixing. |
Rust and Corrosion Prevention |
Cutting fluids should protect the tooling, machine, and work piece
against rust and corrosion. Cutting fluids should leave a small residual
film that remains after the water has evaporated. |
Cutting fluids can be broken into four main categories: straight cutting
oils, water miscible fluids, gasses, and paste or solid lubricants. Two of the three
(chemical-based and emulsions) are primarily water. Water quality has a large
effect on the coolant. Water that is very hard (high mineral content) can cause
rust, stains, and corrosion of machines and work pieces. Water can be deionized
to remove the impurities and minerals.
Water is the best fluid for cooling. It has the best ability to carry heat
away. Water, however, is a very poor lubricant and causes rust.
Oil is great for lubrication but very poor for cooling. Oil is also
flammable.
You can see that water and oil have some great strengths but also some
great weaknesses. If water and oil are combined, we get the best of both and
minimize the weaknesses. Water-soluble fluids have been developed that have good
lubrication, cooling ability and rust and corrosion resistance. These fluids
are usually mixed in the shop. It is crucial that the mixing directions and
concentrations are followed very closely to get the maximum benefit from the
coolant.
Water Miscible Cutting Fluids
 |
Emulsions
Emulsion is a term that describes soluble oils. An emulsion is a suspension
of oil droplets in water. Soluble oils are mineral oils that contain
emulsifiers. Emulsifiers are soap-like materials that allow the oil to mix with
water. Emulsions (soluble oils) when mixed with water produce a milky white
coolant. Lean concentrations (more water-less oil) provide better cooling but
less lubrication. Rich concentrations (less water- more oil) have better
lubrication qualities but poorer cooling.
There are different types of soluble cutting fluids available including
extreme pressure soluble oils. These should be used for extreme machining
conditions where it is necessary to reduce friction where the tool and work
piece contact each other.
Chemical Fluids
Chemical coolants are also miscible cutting fluids. Chemical cutting fluids
are pre-concentrated emulsions that contain very little oil. Chemical fluids mix
very easily with water. The chemical components in the fluid are used to enhance
the lubrication, bacterial control, rust, and corrosion characteristics. There
are several types of chemical coolants available, including coolants for extreme
cutting conditions.
Inactive chemical cutting fluids are usually clear fluids with high rust
inhibition, high cooling, and low lubrication qualities. Active chemical fluids
include wetting agents. They have excellent rust inhibition and moderate
lubrication and cooling properties. Some contain sulfur or chlorine additives
for extreme pressure cutting applications.
Semi-chemical Coolants
Semi-chemical fluids are a combination of a chemical fluid and an emulsion.
They have a lower oil content but more emulsifier. This makes the oil droplets
much smaller. They have moderate lubrication and cooling and high rust
inhibition properties. Sulfur, chlorine, and phosphorous are sometimes added to
improve the extreme pressure characteristics.
Straight Cutting Oils
Straight cutting oils are not mixed with water. Cutting oils are generally
mixtures of mineral oil and animal, vegetable, or marine oils to improve the
wetting and lubricating properties. Sulfur, chlorine, and phosphorous compounds
are sometimes added to improve the lubrication qualities of the fluid for
extreme pressure applications. There are two main types of straight oils: active
and inactive.
Inactive Straight Cutting Oils
Inactive oils contain sulfur that is very firmly attached to the oil. Very
little sulfur is released in the machining process to react with the work piece.
Mineral oils are an example of straight oils. Mineral oils provides excellent
lubrication, but are not very good at heat dissipation (removing heat from the
cutting tool and work piece). Mineral oils are particularly suited to nonferrous
materials, such as aluminum, brass, and magnesium. Blends of mineral oils are
also used in grinding operations to produce high surface finishes on ferrous and
nonferrous materials.
Active Straight Cutting Oils
Active oils contain sulfur that is not firmly attached to the oil. The sulfur
is released during the machining operation to react with the work piece. These
oils have good lubrication and cooling properties. Special blends with higher
sulfur content are available for heavy duty machining operations. They are
recommended for tough low carbon and chrome-alloy steels. They are widely used
in thread cutting. They are also good for grinding as they help prevent the
grinding wheel from loading up. This increases the life of the grinding wheel.
Gasses
Cutting oils and water miscible types of cutting fluids are the most widely
used. Gasses are sometimes use. Compressed air and inert gasses are sometimes
used. Carbon dioxide, Freon, and nitrogen are also used
sometimes.
Paste and Solid Lubricants
Waxes, pastes, soaps, graphite, and molybdenum disulfide may be used. These are
generally applied directly to the work piece or tool, or in some cases,
impregnated directly into a tool, such as a grinding wheel. One example would
be lard. Many experienced journeymen recommend lard for tapping.
The Use of Cutting Fluids in Drill
Press Operations  |
The coolant should be aimed at the area where the tool contacts the work. It
should be flooded so that as much fluid as possible reaches the cutting edges.
The operator should withdraw the tool occasionally to remove the chips. The best
method is the use of tools that have integral oil holes. This means that various
tools are available that feed the coolant through the tool and directly to the
cutting edge (see Figure 1). This also helps wash the chips out of the hole.
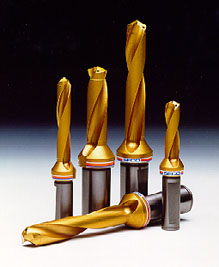 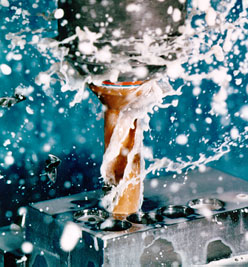
Figure 1 Oil hole drills will supply cutting fluid
directly to the cutting edges of the drill.
The Use of Cutting Fluids in Milling
Operations |
Two nozzles should be used whenever possible in milling operations. One
nozzle
should be in front of the cutter and one behind. Together they cool the tool and
the work piece and wash the chips away.
The Use of Cutting Fluids in Turning
Operations |
In a turning operation, the coolant must be supplied to the area where the
chip is being produced. For turning and facing operations, the nozzle should be
directed so that the coolant is supplied directly over the tool. In heavy-duty
cutting, two nozzles would be advisable, one above and one below the tool (see
Figure 2).
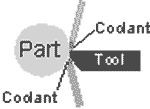
Figure 2 For heavy cutting, it is advisable to have cutting fluid directed
at the top and bottom of the cutting area.
The Use of Cutting Fluids in Grinding
Operations  |
Grinding produces a great deal of heat because the wheel contains thousands
of small cutting edges, each producing heat as it cuts. Flood coolant is most
appropriate when grinding. When possible, use two nozzles for flood coolant, one
on the left and one on the right of the wheel. Keep the nozzles as close to the
work as possible. It is recommended that you use a dummy block on the side of
the workpiece. This helps get an adequate supply of coolant to the work at the
start of the cut.
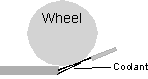
Figure 3 No dummy block was used in
this case, so at the start of the cut there is very little coolant when
the cut begins.
|
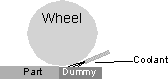
Figure 4 In this figure a dummy
block was used. This assures adequate coolant at the start of the cut.
|
In cylindrical grinding, a fan-shaper nozzle that is slightly wider than the
wheel should be used. This assures that the entire grinding surface is flooded.
When internal grinding, the wheel should be as large as possible. The wheel
should be approximately 75% of the diameter of the hole in the workpiece. This
does not allow much room to get coolant into the bore. Make sure that an
adequate amount of coolant flows into the bore.
Material |
Milling |
Drilling |
Tapping |
Turning |
Aluminum |
Soluble oil (96% water) or mineral oil |
Soluble oil (70-90% water) |
25% sulfur-based oil mixed with mineral oil |
Mineral oil with 10% fat (or) soluble oil |
Brass |
Soluble oil (96% water) |
Soluble oil |
10-20% lard oil with mineral oil |
Mineral oil with 10% fat |
Bronze |
Soluble oil |
Soluble oil |
30% lard with mineral oil |
Soluble oil |
Alloy Steels |
10% lard oil with 90% mineral oil |
Soluble oil |
30% lard oil with 70% mineral oil |
25% sulfur base oil with 75% mineral oil |
Cast Iron |
Dry |
Dry |
Dry or 25% lard oil with 80% mineral oil |
Dry |
Malleable Iron |
Soluble oil |
Soluble oil |
Soluble oil |
Soluble oil |
Copper |
Soluble oil |
Soluble oil |
Soluble oil |
Soluble oil |
Low Carbon and Tool Steels |
Soluble oil |
Soluble oil |
25-40% lard oil with mineral oil |
25% lard oil with 75% mineral oil |
Coolant Maintenance
 |
Maintain the coolant system correctly during and after mixing. Be sure to
allow for evaporation. To mix coolants, in a separate pail, add the desired
amount of water. Next add the desired amount of coolant. Pour the diluted mixture into
the machine sump. Remove floating tramp oils regularly. These oils cut off
oxygen from the coolant, and some may mix with the coolant, reducing its
effectiveness. Hydraulic fluids and other oils are major contributors to
rancidity. An oil skimmer will remove these oils efficiently, extending the sump
life. Keep the dirt levels low. This is particularly true in grinding
applications because high swarf promotes bacteria growth and leads to a poor
finish. Keep foreign matter out of the coolant in the sump. Cigarette butts and
similar trash will foul the coolant and clog the system. Try to aerate the coolant
when not in use so that the biocides can do their job. Test and evaluate coolants on
an ongoing basis. By using a refractometer (Figure 5), checking coolant dilution
levels is quick and easy. Refractometers are hand held, lightweight, portable
instruments used to determine the concentration of water soluble fluids, such as
machine tool coolants, heat treating fluids, hydraulic fluids, plating baths,
detergents, antifreeze, battery acid, and bodily fluids.
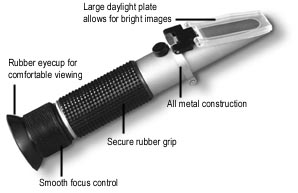
Figure 5 A refractometer is used to measure
coolant dilution.
Refractometers are very easy to use. Just place a few drops of fluid on the
prism and hold the unit up to a light source. Look into the eyepiece and read
the scale. To calibrate, just make sure the prism is clean and place a few drops
of tap water on the prism. The separation line should be on zero. If not, turn
the adjustment screw until it is.
Remember, refractometers read on a Brix scale not actual percent. To get the
actual percentage you must multiply the refractometer reading by your coolant's
refractive index (on product data sheet). With most soluble oils the index is 1,
so a Ref. reading of 5 x index of 1 = 5% concentration. However, many
semi-synthetics, synthetics, grinding fluids, and some soluble oils can have a
refractive index from 1.5 to 3. So a Ref. reading of 5 x index of 1.75 = 8.75%
concentration. This is most critical with solutions designed to be run at lower
concentrations, which have high indexes.
Always dispose of coolants properly. With all coolants, consult your
local, state or EPA regulatory office for guidelines.
Top
|