Lathe
Operations - Tapers with a Taper Attachment
|
Setting the taper attachment to cut an accurate taper can be difficult. Once you have
initially set up the taper attachment according to the text, the taper attachment setting
will need to be refined. There are a number of ways to check the taper bar settings for
accuracy.
- The most common way to check the taper bar setting for accuracy is the trial and error
method. Move the carriage 1 to 2 inches to the right of the taper start position.
This should be done at every pass to remove the backlash in the taper attachment. Feed the
tool into the trial cut depth. Make a 1-inch-long trial pass. Check the
start and end diameters of the taper at the 1-inch-long interval. The difference in the
diameters should be the required taper per inch. Move the cross slide extension to the
pivot point of the taper bar and adjust the taper attachment accordingly.
|
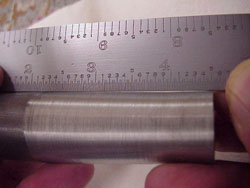
Figure 1 |
Note: Using a straight edge, check to see
that the entire length of the turned area is tapered(Figure 1). There should not be
any open space along the straight edge if the entire length is tapered. If the entire
length is not tapered, there is still backlash in the taper attachment. Try starting the
cut back farther to alleviate all of the backlash. The trial and error method of taper
attachment adjusting is acceptable as long as you have plenty of excess stock to work
with.
- The dial indicator method is a better method of checking the accuracy of the taper bar
setting, especially when there is not an excess amount of surplus stock. Set up a test bar
or your workpiece in the machine. Set up a dial indicator on the compound rest or the
cross slide extension as shown in Figure 2.
|
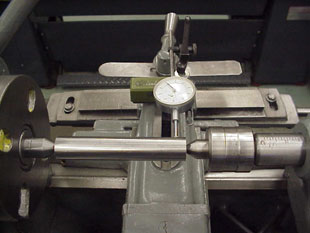
Figure 2 |
Now set up an indicator to measure the amount of carriage movement as shown in Figure
3. |
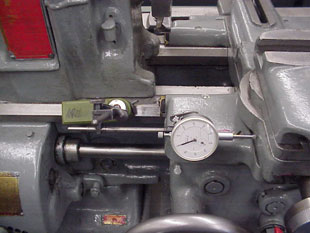
Figure 3 |
Move the carriage until the dial indicator on the compound rest begins to read a
consistent amount of travel. Set this indicator to zero. Reset the indicator that is
keeping track of carriage movement to zero. Move the carriage 1.00 inch. The reading on the cross slide indicator should be that of the required taper per inch divided
by 2 (Figure 4). If it is not, move the cross slide extension to the pivot point of the
taper bar and adjust the taper attachment accordingly. |
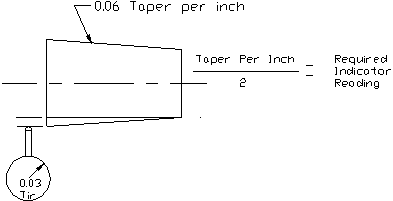
Figure 4
|
- The digital readout is the best method of checking the accuracy of the taper bar
setting. Set up the taper attachment according to the taper bar setting. Make sure
that the X axis digital readout is set to Diameter rather than Radius
(Figure 5).
|

Figure 5 |
Move the carriage until the X axis readout begins to read a consistent amount
of travel. Reset both axis displays to zero. Move the carriage 1.00 inch. Note the X axis
diameter coordinate. When the taper bar is set properly, the X axis diameter readout over
one inch of carriage travel should be that of the required taper per inch.
Top
|