Inspection Methods -
The Steel Rule
|
Steel
Rule Measurement
With the technical advances being made, most people are inclined to
think that complex electrical measuring equipment is needed to inspect parts
made by the machinist or toolmaker. Although this is true in some cases,
the majority of the parts that are made do not require this sophisticated
equipment.
One tool that is very common in the machine shop area that is
not a
high precision measuring tool is the steel rule (Figure 1). |

Figure 1 |
The rigid six-inch rule is a common measuring tool found
in the machine shop. The rule is a strip of metal graduated in inches and
fractions of an inch to give actual measurements.
When tolerances of fractional dimensions are required, the steel rule
is used. The most commonly used steel rule is the 6" rule. Although
rules come in 6-inch increments (Example: 6", 12", 18",
24", and 36" lengths), the 6-inch rule is the most popular
because it fits into the apron pocket easily. It also comes in various
widths and thicknesses to meet varying requirements, as will be seen in the
slide series.
Rules vs. Scales

The terms "rules" and "scales" are used in
different ways by different workers, sometimes causing confusion. While
some manufacturing workers do not differentiate between these terms,
others use the term "rule" when referring to a measurement tool
that provides actual linear measurements. In other words one inch on the
rule represents exactly one inch of linear distance. On the other hand, to
these workers, a scale is a measurement tool in which an actual measured
linear distance
represents another imaginary (smaller or larger) linear
distance. For example, on an architect's scale (Figure 2), one inch of
measured distance may represent one foot of actual linear distance. When
this principle is in operation, a "key" should indicate the
ratio of measured distance to actual distance or "scale" that is
being used. |
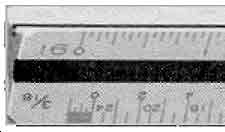
Figure 2: Architectural Scale |
Increment Divisions

There are four basic divisions that are found on a fractional inch
rule. These are: 1/64, 1/32, 1/16 and 1/8 of an inch.
Let's look at each graduation a little closer. A 1/64" graduate
scale means that in a 1-inch length, there are 64 lines dividing that inch (Figure 3). |
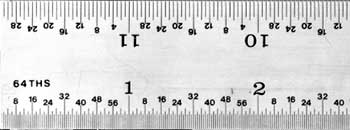
Figure 3
|
These are the smallest graduations on the rule, therefore making the
accuracy of a steel rule 1/64". This is sometimes argued by some of
the metal workers who say they can measure to within ±.003 with the rule.
They are right for they have worked with it a long time and have become
masters at reading the graduations. However, the rule is only intended to
measure to 1/64" accuracy, and other instruments are used to measure
to closer tolerances.
The next set of graduations is the 1/32" scale, which divides a
1-inch length into 32 divisions. A 1/32 division is equal to 2/64
divisions (Figure 4). |
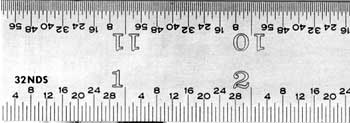
Figure 4
|
The 1/16" scale divides a 1-inch length into 16 divisions and is a
total of 4/64 or 2/32 graduations (Figure 5). |
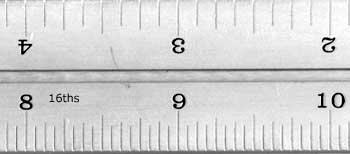
Figure 5
|
The 1/8" scale divides a 1-inch length into 8 equal divisions and
is a total of 8/64, 4/32, or 2/16 graduations (Figure 6). |
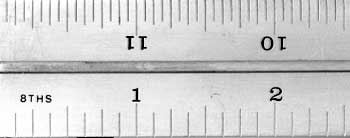
Figure 6
|
As you can see, a combination of two or more of the various graduations
will make up a larger graduation. The same holds true with graduations
larger than 1/8". Any combination of the four different sized
graduations will give a reading up to the 1-inch length. Figure 7 is a
decimal equivalent chart that shows all the various fractions possible in
one inch.
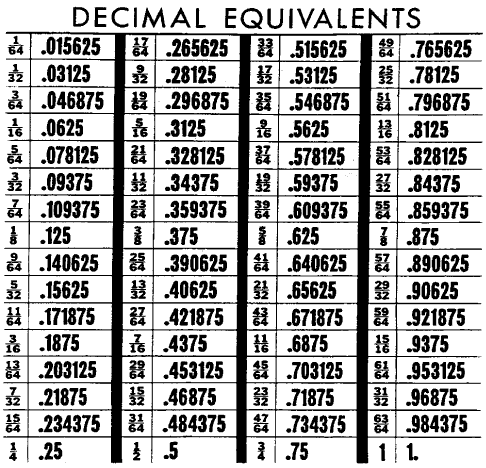
Figure 7
As can be seen on the chart, 3/8" is only given as 3/8". It
is not 24/64", 6/16", or 12/32". Any of these fractions
does equal 3/8", but it is reduced to its lowest terms. Another
example would be 7/16". This could be given as 14/32" or
28/64", but these are not in their lowest terms.
Also, the 1/2 division, the 3/4 division and 1-inch division are not
read as 8ths, 64ths, 32nds, or 1/16, even though they are made from these
combinations. They are read as 1/2", 3/4", or 1 inch. Now that
you have this information under your belt, let's look at how a rule should
be used.
To get the full accuracy out of a rule, it is important to use it
correctly. Never use the end of the rule to align with the edge of the
work for a measurement (Figure 8). The end of a rule is often rounded off
from misuse, and a true measurement will not be made. |
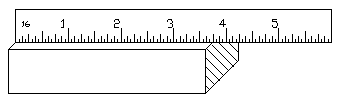
Figure 8 |
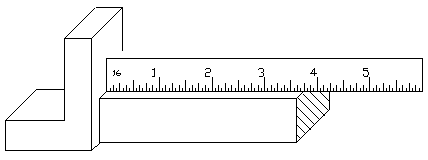
Figure 9 |
Even if the workpiece is held firmly against a reference surface, such
as an angle plate (Figure 9), this will not assure an accurate measurement
if the end of the rule is worn off.
|
To offset this, use an inch graduation as a reference point on the rule
(Figure 10). Precision and reliable measurements are possible this way.
With the graduation directly on the edge of the work, and by not using the
end of the rule, wear is inconsequential. |
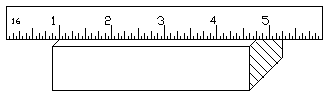
Figure 10 |
When measuring a length, the rule must be kept in a straight line
parallel to the centerline of the work. If it is tilted, the measurement
will be longer than the actual part. See Figure 10.

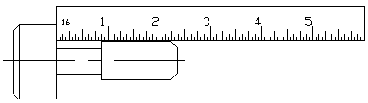
Correct
|
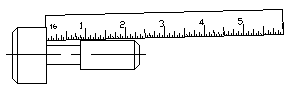
Incorrect |
Figure 10 |
One other important factor in using the rule is to be aware of
parallax. This is an observation error from the person measuring or
holding at the part in relation to the part being held.
|
|
Incorrect
(Rule Lying Flat)
|
Correct
(Rule Standing on Edge)
|
Figure 11 |
In Figure 11, the drawing on the left shows an incorrect way of measuring, and parallax
is greatly increased because of the thickness of the rule. The graduations
do not come in direct contact with the work. The arrows pointing to the
right and left will cause parallax, and even though the arrow pointing
straight up is the correct way to view the rule, there is a chance for
error in reading due to the thickness of the rule.
The drawing on the right shows the rule on its edge. As can be seen,
the graduation comes in contact with the work, which is the correct way of
measuring. Although the arrows pointing to the right and left will cause
an improper reading, it will not be as great an error as when the rule is used
in the manner shown in the drawing on the left. The proper way is to view the graduation straight
up as the center arrow illustrates.

|