The engine lathe is a precision machine tool and must be treated with
great care. Regular cleaning and
maintenance will help to assure that the lathe will maintain its service
life and accuracy for many years. This unit will cover basic lathe
maintenance. The procedures you find within this document should be able
to be performed by apprentice or beginning machine tool students. Lathe
maintenance that requires more extensive disassembly should only be done
by, or under the supervision of, qualified personnel.
Drive
Belts
The drive belts supply power from the motor to the spindle. Access
to the drive belts is gained by removing the end guard on the
headstock (Figure 1). Make sure that all power is locked out
before removing any guards. |

Figure 1 Head stock end guard.
|
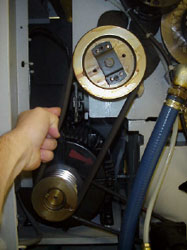
Figure 2 Each belt should have
approximately the same amount of tension.
|
Drive belts come in matched sets and should only be replaced with
a matched set of belts. Visually inspect the drive belts for
excessive wear and cracking. If you notice that one or more of the
drive belts appear to be excessively worn or cracked, bring this to
the attention of the instructor. Check the belt tension by applying
finger pressure to each belt at a point midway between the two
pulleys (Figure 2). For correct tension a deflection of about 3/8 of
an inch should be evident in each belt. If the amount of deflection
is more than 3/8 of an inch in any one or more of the belts, bring
this to the attention of the instructor. |
Gib
Adjustment
All lathes employ precision slide ways. The saddle, cross slide,
and the compound slide all ride along a box slide way or dovetail
slide way. After time the parts that ride along the slide ways begin
to wear. To compensate for this wear, machine tools are equipped
with adjustable parts called gibs that allow you to eliminate the
space that has been created by the wear between the slide ways.
(Figure 3). |
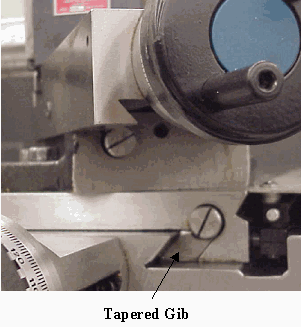
Figure 3 A tapered gib located
on the cross slide of a lathe |
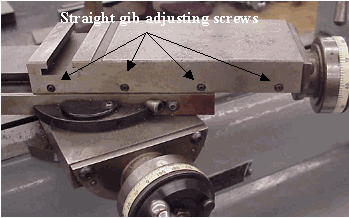
Figure 4 A compound slide
utilizing a straight gib
|
There are two types of gibs, straight gibs and tapered gibs.
Straight gibs are adjusted by screws spaced out along the length of
the gib. The screws push the gib in to create more contact with the
sliding mechanisms (Figure 4). |
Tapered gibs use two screws. The screws are located in each end of
the tapered gib. One screw acts as an adjustment while the other
screw acts as a locking mechanism. Because tapered gibs are wider on
one end than the other, they slide in or out creating more or less
contact between the sliding mechanisms (Figure 5). |
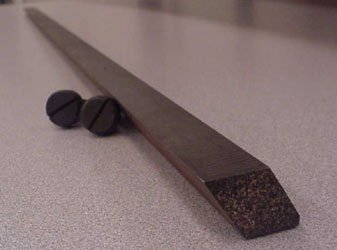
Figure 5 Tapered gib with
screws
|
Cross
Slide Gib Adjustment
Wear in the cross slide ways must be adjusted by using the screw
on the front face of the cross slide. (Figure 6). |
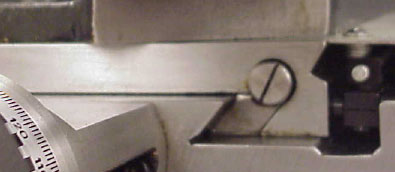
Figure 6 Front gib screw
|
The procedure is to first loosen the similar gib screw on the rear
face of the cross slide (Figure 6a), then re-tighten the front screw
to lock or adjust the gib in its new position.
After the adjustment, traverse the cross slide over its entire
travel to be sure of smooth, even operation. |
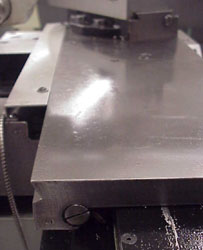
Figure 6a Rear gib screw
|
Compound
Slide Gib Adjustment
Wear in the compound slide ways must be adjusted by using the
screw on the front face of the compound slide. (Figure 7).
The procedure is to first loosen the similar gib screw in the
rear face of the tool slide, then re-tighten the front screw to lock
or adjust the gib in its new position. After making the adjustment,
traverse the compound slide over its entire travel to be sure of
smooth, even operation. |
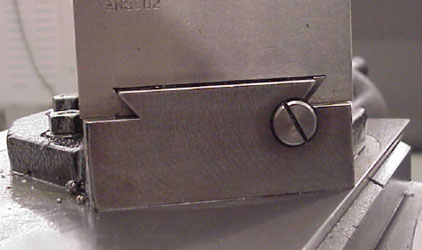
Figure 7 Tool slide gib screw
|
Wipers
Pads
Most lathes are equipped with wiper pads (Figure 8). Wiper pads
are typically made of felt that will hold oil.
Wipers are designed to keep out small chips and dirt between the
slides and the ways. Wipers are saturated with oil to catch the fine
particles of dirt or debris before they get between the two sliding
surfaces. The wipers should be removed, cleaned, and re-saturated
with oil regularly. You should never use compressed air for cleaning
a lathe. Compressed air will push the fine particles trapped in the
wiper between the mating surfaces of the slides, causing
premature wear on these precision surfaces. |
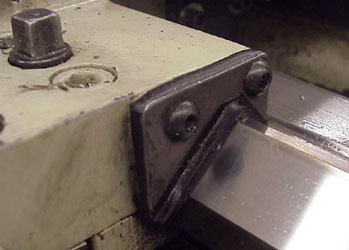
Figure 8 Wiper pads
|
Adjusting
the Tailstock Clamp
The lock position of the bed clamp lever on the tailstock is
adjustable and should be located before
top dead center (Figure 9). |
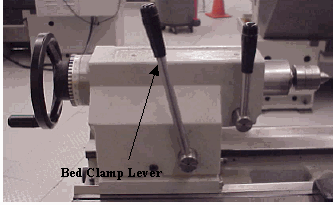
Figure 9 The lock position of
the bed clamp lever on the tailstock
|
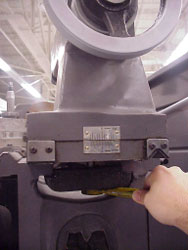
Figure 10 Tailstock locking lever
adjustment bolt
|
The lever is adjusted by a self-locking bolt located on
the underside of the tailstock front clamp plate and between the
bedways (Figure 10). Turn the bolt clockwise to increase the
clamping action. Lathes may also be equipped with an auxiliary bolt
on the tailstock. This bolt is used to give additional clamping
action when required. It does not require any adjustment. |
End
Gearing and Backlash
The end gearing on the lathe connects the spindle rotation with
the feed and threading rods (Figure 11).
|
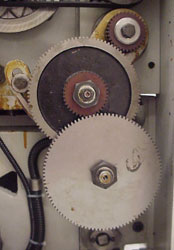
Figure 11 Lathe end gearing
|
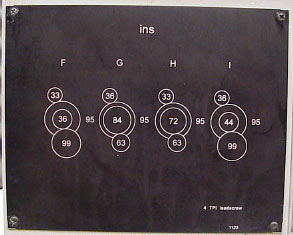
Figure 12 End gear chart
|
The gears supplied with a lathe allow the operator to obtain an
extensive range of feeds, metric threads, threads per inch, module
and diametral pitch threads. To cut threads over a broad range, the
lathe operator will need to make changes to the end gear train.
Basic lathe setup and operation includes being able to properly
change the gears in the train. Most lathes are equipped with charts
that explain the gear positioning for certain types and ranges of
threads (Figure 12). |
When the proper gears have been selected and set in the gear
train, the mounting or clamping bolts should be lightly snugged in
place with a strip of paper or feeler stock placed between the gears
(Figure 13). |
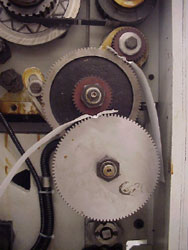
Figure 13 Setting the backlash in
the end gear train
|
The gears should then be pushed together against the paper shim. The
clamping bolts should then be tightened. Remove the shim. The space left
between the gears, where the shim was placed, is known as backlash. On most
lathes the backlash amount should be between 0.007 and 0.011 inches. If
the gears are noisy, more backlash space should be made between the gears.
Finish the backlash adjustment by placing a small amount of lubricant on
the gear train.
|